Rohrvortriebe im Grenzbereich
Extreme Geologie, enge Kurven, geringe Überdeckungen: Bei drei Langstreckenrohrvortrieben in den Schweizer Alpen ging es bis an die Grenzen dessen, was derzeit mit Microtunnelling-Technik machbar ist. Zum Teil auch darüber hinaus.
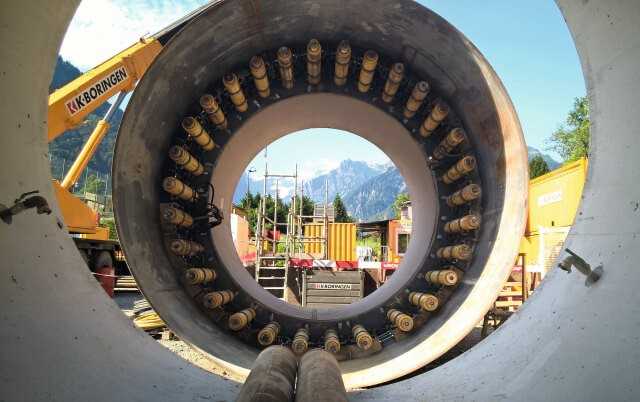
Nur Microtunnelling sinnvoll
Zentrale Bauwerke solcher Anlagen sind Stollen, die mit ausreichend Volumen und der nötigen Höhendifferenz den Strom erzeugenden Turbinen das Wasser zuführen. Der Bau dieser Stollen wurde als Rohrvortrieb geplant. „Alle drei Projekte wären ohne die Anwendung von Microtunnelling-Technik wirtschaftlich nicht realisierbar gewesen“, sagt Dr. Stefan Trümpi. Er ist Inhaber und Geschäftsführer der Jackcontrol AG und an den Bauvorhaben als Planungsbüro und vortriebsbegleitend beteiligt. Ebenso die Firma K-Boringen aus Belgien, die jeweils den Auftrag für die Rohrvortriebe erhielt und bei den drei Maßnahmen die komplette Systemausrüstung von Jackcontrol, bestehend aus der Hydraulischen Fuge und dem Vortriebsüberwachungssystem, einsetzte.
Kraftwerk Doppelpower: Schwieriger Baugrund
Der erste Vortrieb gehörte zum Kraftwerk Doppelpower und war mit einer Länge von 1.700 m und einer Höhendifferenz von 36 m geplant. Die Vortriebsrohre haben bei einer Länge von 4 m einen Innendurchmesser von 3.000 mm und eine Wandstärke von 400 mm. Die Trasse verläuft durch ein Bergsturzgebiet mit extremer Geologie. „Die Korngrößenverteilung reichte von wenigen zehntel Millimetern bis hin zu hausgroßen Felsblöcken in chaotischer Durchmischung“, beschreibt Dr. Stefan Trümpi den Baugrund. Die Festigkeit des Kalkgesteins betrug bis zu 170 MPa. Der Vortrieb verlief vollständig im Grundwasser mit einem Druck von 2 bis 3 bar im Durchschnitt und Spitzenwerten bis zu 7 bar. „Da es sich bei der Geologie um Bergsturzmaterial handelte, konnten wir nicht von einem stabilen Ringspalt ausgehen. Wir mussten damit rechnen, dass Boden auf die Rohre drückt und die Reibungskräfte erhöht“, so der Projektleiter von K-Boringen, Stijn Philips. Die unterschiedlichen Wasserdrücke hatten zur Folge, dass sich stellenweise im Ringspalt eine Strömung ausbildete, die das Bentonit ausspülte und so ebenfalls die Mantelreibung des Rohrstranges und den Bentonitverbrauch erhöhte.
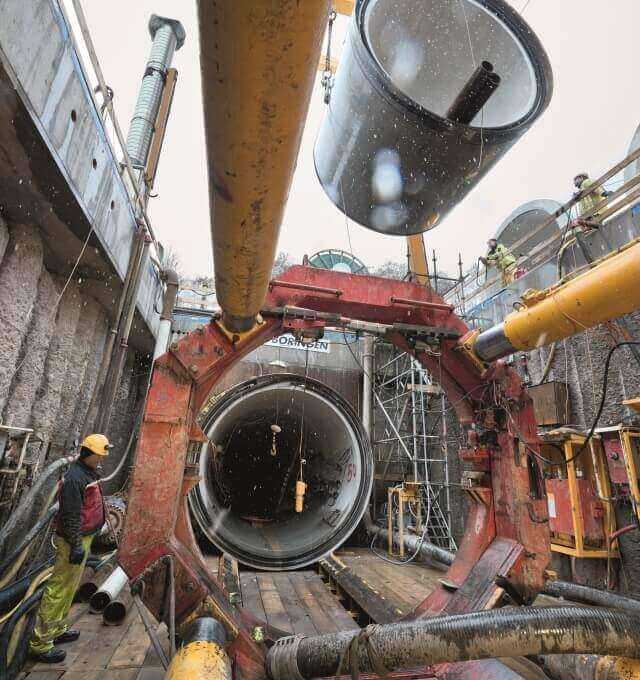
Stecken geblieben im Berg
Nach 200 m Vortrieb entschloss man sich seitens der Vortriebsfirma und der Bauherrschaft, über einen Serviceschacht das Schneidrad zu wechseln, da die Festigkeit des Gesteins größer war als vermutet. Anschließend lief der Vortrieb bis zur Länge von etwa 1.100 m relativ störungsfrei. Dort kam es zu einer Schneidradblockade, deren Ursache bis heute nicht zweifelsfrei geklärt ist. Nach einer manuellen Räumung des Bohrkopfes und dem Entfernen von fußballgroßen Steinen konnte dieses Problem innerhalb einer Woche gelöst werden.
Nach 60 weiteren Vortriebsmetern wurde eine Kluft mit Fremdmaterial angebohrt, das auf die Rohre drückte und zu einem Feststecken des Rohrstranges führte. Daraufhin wurden in diesem Bereich die Rohre mit Kernbohrungen perforiert und über die Öffnungen der Ringspalt freigespült. Nach drei Monaten konnte der Vortrieb fortgesetzt werden, bis er nach weiteren etwa 80 m erneut zum Stillstand kam. Grund war diesmal eine angebohrte Wassersäule, die einen Druck von 7 bar erzeugte. Die Vortriebsmaschine war jedoch nur für einen Wasserdruck von 4 bar ausgelegt. Der Versuch, in der Maschine mit Druckluft einen Überdruck von 3 bar zu erzeugen und damit den zu hohen Außendruck auszugleichen, gelang, und der Vortrieb konnte noch einmal fortgesetzt werden. Bei 1.300 m verkeilte sich der Rohrstrang jedoch genau an der Stelle der angebohrten Wassersäule und steckte erneut fest. Die Überdeckung an dieser Stelle beträgt 128 m.
„Richtig guten Job gemacht“
Eigentlich hatte die Planung ein solches Szenario berücksichtigt. Die Vortriebsmaschine war mit einem Push-Modul ausgerüstet, das in einem solchen Fall das Wechseln vom Rohrvortrieb auf Tübbingbauweise ermöglicht. Der Auftraggeber entschied jedoch, den Vortrieb abzubrechen und den Tunnel von der Gegenseite in bergmännischem Vortrieb fertigzustellen und die feststeckende Vortriebsmaschine zu bergen. Diese Maßnahme läuft derzeit noch.
„Obwohl der Vortrieb beim Kraftwerk Doppelpower nicht fertig gestellt werden konnte, hat K-Boringen bei dieser Maßnahme einen richtig guten Job gemacht“, lobt Dr. Trümpi. „Mit aufrechtem Haupt und der Fahne im Wind hat die Mannschaft das gemacht, was möglich war.“ Diese Leistung hat letztlich die Bauherren der folgenden Maßnahmen soweit überzeugt, dass sie mit der Firma K-Boringen auch die nächsten Vortriebe machen wollten – zumal das Unternehmen mittlerweile über wertvolle Erfahrungen in den Böden der Region gesammelt hatte. „Und der Erfolg bei den nachfolgenden beiden Vortrieben hat dem auch Recht gegeben“, so Trümpi.
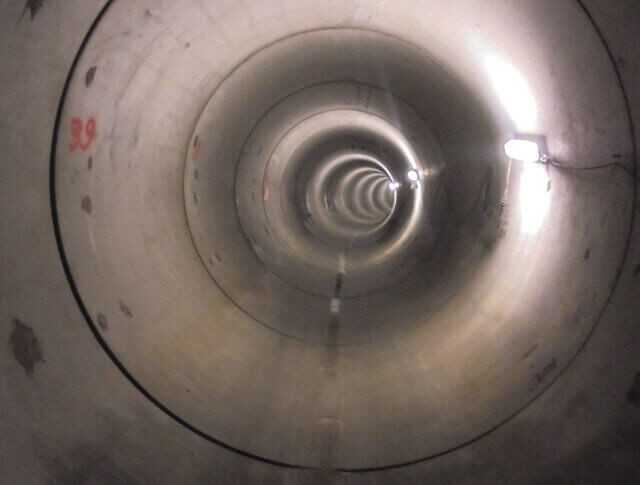
Kraftwerk Rufi: Gefahr von Niederbrüchen
Extrem um die Kurve
Eine große Herausforderung war es, unter diesen Umständen die bestehende Infrastruktur zu unterqueren. Dazu gehörte zum einen ein Kraftwerkskanal, der in Betrieb mit einer Überdeckung von 70 cm unterfahren werden musste. „Dabei ist auch etwas Bentonit ins Wasser ausgetreten“, konstatiert Dr. Trümpi. Im weiteren Verlauf war ein Abwasserkanal zu unterqueren, was nach entsprechenden Sicherungsmaßnahmen ohne Probleme gelang. Schließlich waren bei der Kreuzung einer Bahnlinie Setzungen des Gleiskörpers unbedingt zu vermeiden. Um dies millimetergenau zu dokumentieren, kam ein System zur Überwachung von Oberflächensetzungen der Firma VMT zum Einsatz. „In diesem Bereich wurde beim Vortrieb der Stützdruck an der Ortsbrust erhöht, mit vollem Schneidrad gefahren und an der Oberfläche Aufschüttungen als zusätzliche Auflast hergestellt“, beschreibt Stijn Philips. Gebohrt wurde nur nachts, wenn keine Züge unterwegs waren.
Spektakulär bei diesem Vortrieb war eine zu durchfahrende Raumkurve mit einem minimalen geplanten Raumradius von 260 m. „Bei dem Rohrdurchmesser DN 3200 und einer Rohrlänge von 3 m ist das extrem, und nach meinem Kenntnisstand der bisher engste Radius, der mit solchen Rohren je gefahren wurde“, sagt Dr. Stefan Trümpi. Um dies mit der eingesetzten Vortriebsmaschine überhaupt realisieren zu können, hatte K-Boringen zwischen Maschine und dem ersten Vortriebsrohr zusätzliche Steuerzylinder installiert, die manuell bedient wurden. Die Hydraulische Fuge von Jackcontrol kam hier in besonders dicker Ausführung mit einem Schlauchdurchmesser von 50 mm zum Einsatz. „Am Schluss der Raumkurve wurde sogar eine Teilklaffung in der Rohrfuge in Kauf genommen“, so Trümpi weiter. „Das wurde aber vom Überwachungssystem und bei der Bestimmung der zulässigen Vortriebskräfte berücksichtigt.“ Schließlich wurde der Vortrieb erfolgreich und ohne feststellbare Rohrschäden abgeschlossen.
Kraftwerk Cotlan: Gute Leistung trotz widriger Bedingungen
Der dritte Vortrieb gehörte zum Kraftwerk Cotlan und hatte eine Länge von 640 m. Die Vortriebsrohre mit 3.800 mm Außen- und 3.000 mm Innendurchmesser und einer Länge von 4 m entsprechen denen, die auch beim Vortrieb für das Kraftwerk Doppelpower zum Einsatz kamen. Für die Herstellung dieser Rohre hatte die Firma Gollwitzer ganz in der Nähe der Baustellen eine Feldfabrik eingerichtet. Rohrproduktion vor Ort hatte große logistische Vorteile. Allein der Transport der 43 to schweren Bauteile mit den erforderlichen Sondergenehmigungen und der obligatorischen Begleitung sowie die pünktliche Lieferung „just in time“ wurde durch den kurzen Weg erheblich vereinfacht und sparte Lagerplatz auf der Baustelle.
Die Vortriebstrasse beim Kraftwerk Cotlan beinhaltet eine horizontale und eine vertikale Kurve mit Radien von 500 und 1.000 m. Die Geologie ist ähnlich der beim Kraftwerk Rufi. Auch hier hatte es K-Boringen mit instabilem, abrasivem Boden und mit geringen Überdeckungen zu tun.
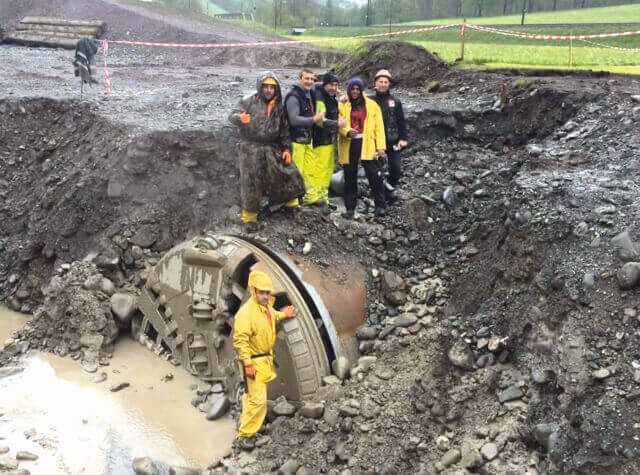
Die ersten 300 m Vortrieb verliefen unter dem Fluss. „Das war für uns ein besonderes Risiko. Denn hier war es praktisch unmöglich, an der Maschine zu arbeiten oder Werkzeuge zu wechseln“, so Stijn Philips. Zwar waren die technischen Voraussetzungen vorhanden, um unter Druckluft in den Bohrkopf einzusteigen, bei der geringen Überdeckung von 3 bis 4 m wäre jedoch die Gefahr von Ausbläsern und damit das Risiko für das Personal viel zu hoch gewesen.
Die Vortriebsleistung lag – ähnlich wie beim Kraftwerk Rufi – zwischen 60 und 100 m pro Woche. Gearbeitet wurde 24 Stunden an sieben Tagen in der Woche. „Bei diesem Rohrdurmesser und in dieser Geologie ist das schon eine bemerkenswerte Leistung“, so das Urteil von Dr. Trümpi.
Erfahrungen genutzt
„Bei dieser Maßnahme haben uns die Erfahrungen vom Kraftwerk Rufi sehr geholfen“, sagt Stijn Philips. So wurden die Maschine und das Schneidrad aufgrund der hohen Abrasivität des Bodens noch einmal zusätzlich mit Aufpanzerungen gegen Verschleiß geschützt. Wie sinnvoll das war, offenbarte sich beim Durchstich. „Der Vortrieb hätte mit Blick auf das Schneidrad nicht viel länger sein dürfen“, betont Philips. „Und wir sprechen hier von 10 oder 20 m!“ Doch nicht nur der Bohrkopf litt unter der Abrasivität des Bodens. Auch die Förderleitungen und die Separieranlagen waren einem hohen Verschleiß unterworfen.
Bei allen drei Projekten kamen die Hydraulische Fuge und das Überwachungssystem von Jackcontrol zum Einsatz. Für Stijn Philips war dies ein wichtiger Schlüssel zum Erfolg. Durch die Druckmessungen in den Rohrverbindungen war während des Vortriebes immer zu erkennen, an welcher Stelle des Rohrstranges erhöhte Reibungskräfte auftraten. Dies eröffnete die Möglichkeit, sehr gezielt Gegenmaßnahmen einzuleiten. Zum anderen ermöglichte die Hydraulische Fuge in dieser schwierigen Geologie maximale Presskräfte zu übertragen. „Als Nebeneffekt hilft die Hydraulische Fuge bei solchen Langstreckenvortrieben die seitlichen Bettungskräfte und damit die Mantelreibung des Rohrstranges, respektive die erforderlichen Vortriebskräfte deutlich zu reduzieren“, ergänzt Dr. Trümpi.
Wertvolle Erkenntnisse
„Bei Doppelpower haben wir die Grenze gefunden, was mit konventionellem Microtunnelling so geht. Wir haben aber viele dieser gemachten Erfahrungen bei Rufi und Cotlan erfolgreich umsetzen können“, ist Trümpi überzeugt. Die Projekte hätten den Erfahrungsschatz der Beteiligten massiv erweitert und damit Grundlagen geschaffen, zukünftige Projekte unter ähnlichen Randbedingungen noch sicherer zu beherrschen. Das Arsenal an Problemlösungsstrategien sei größer geworden, und in den Köpfen seien neue Ideen entstanden, wie man den Herausforderungen bei Langstreckenvortrieben in solchen Geologien begegnen kann.
Rohrpost abonnieren!
Wir graben für Sie nach Neuigkeiten. Die Ergebnisse gibt es bei uns im Newsletter.
Jetzt anmelden!
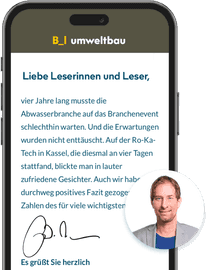
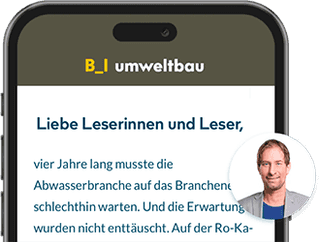
Auch wenn Doppelpower, Rufi und Cotlan keinen revolutionären Durchbruch in eine neue Dimension des Rohrvortriebes darstellen, die Grenzen des Machbaren für dieses Bauverfahren haben sich mit diesen Projekten in der Schweiz ein Stück verschoben, ist sich Dr. Trümpi sicher. Alle drei Projekte wären ohne die Anwendung von Microtunnelling-Technik wirtschaftlich nicht realisierbar gewesen. Insofern sei dieses Bauverfahren bei den drei Projekten eine Schlüsseltechnologie für die zukünftige Energiestrategie der Schweiz. „Und dieser Aspekt ist doch ein Highlight für die grabenlosen Bauweisen“, resumiert Dr. Stefan Trümpi.
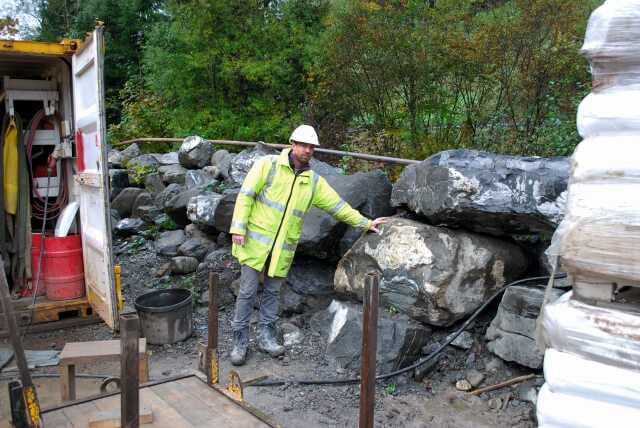
Weiterlesen:
Neueste Beiträge:
Meistgelesene Artikel
Für welche Leistungsart interessieren Sie sich?
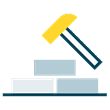
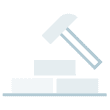
Bauleistungen
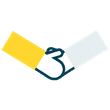
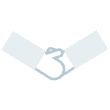
Dienstleistungen
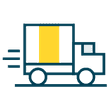
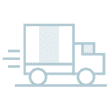
Lieferleistungen
Verwandte Bau-Themen:
Top Bau-Themen:
Aktuelle Termine für unterirdische Infrastruktur
25.08.2025 - 26.08.2025
Seminar Bedarfsorientierte Kanalreinigung10.09.2025
Norddeutsche KanalsanierungstageJetzt zum Newsletter anmelden:
Leitungsbau, Kanalsanierung, Abwasser – erfahren Sie das wichtigste rund ums Thema unterirdische Infrastruktur.