Unwägbarkeiten bei Sammlerneubau gemeinsam bewältigt
Im April 2016 erhielt die Braumann Spezialtiefbau GmbH aus Bottrop den Auftrag über die Ausführung von Rohrvortriebsarbeiten auf der Baustelle „Rue de Neudorf“ in Luxemburg-Stadt. Dies alles in einer sehr schwierigen Geologie in einer Wechsellagerung aus Luxemburger Sand- und Mergelsteinen sowie einem über der geplanten Trasse liegenden einsturzgefährdeten Schmutzwasserkanal DN 1000.
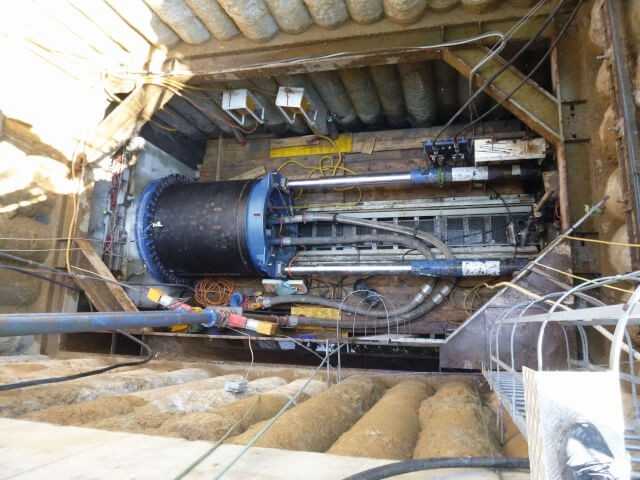
Insgesamt waren 1.340 m Rohrvortrieb DN 1800 in vier Haltungen herzustellen, größte Einzellänge 546 m sowie Kurvenradien zwischen 500 und 700 m. Die Baumaßnahme hat eine Vorgeschichte: So wurde bereits vor rund 10 Jahren ein erster Versuch gemacht, diesen Trassenabschnitt in der Straße Rue de Neudorf im Rohrvortriebsverfahren aufzufahren. Leider kam es bereits auf der ersten Haltung zu einem massiven Bodenentzug, der in einem Tagbruch mitten auf der Straße endete. Aufgrund dieser Erfahrungen wurde die Maßnahme nochmals völlig überplant und im Jahr 2015 erneut ausgeschrieben.
Durch diese Vorgeschichte wurde von Seiten des Auftraggebers sehr großer Wert auf eine sorgfältige Arbeitsvorbereitung gelegt. Nach Abschluss der Arbeitsvorbereitung und Erstellung der ersten Start- und Zielbaugruben konnte im Mai 2016 mit Vortriebsarbeiten der ersten Haltung begonnen werden. Diese Haltung wurde bis August 2016 erfolgreich aufgefahren. Der vorliegende Bericht handelt von den Unwägbarkeiten, die uns auf der zweiten Strecke in Atem hielten, und den Erfahrungen, die aus diesen Unwägbarkeiten gewonnen werden konnten.
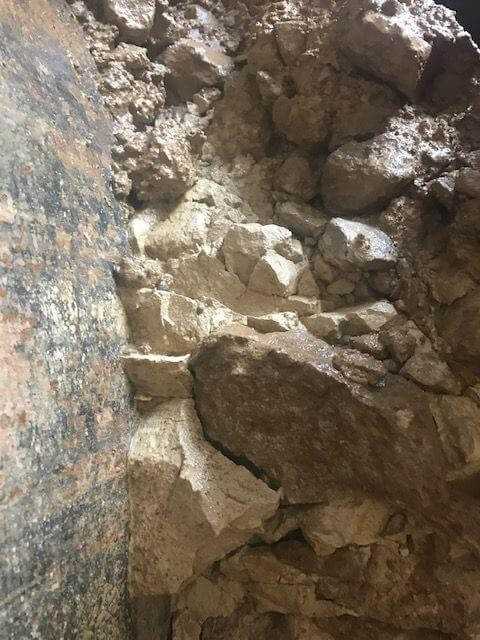
Stillstand beim Vortrieb
Im September 2016 wurde mit dem Vortrieb der zweiten Haltung begonnen. Dann machten wir jedoch mit der Komplexität des Luxemburger Sandsteins Bekanntschaft. Bei Station 165 m kam der Vortrieb plötzlich und unerwartet zum Stillstand. Ursache war eine Zwängung des Rohrstranges, ca. 15 m hinter der Maschine, die zur Zerstörung von zwei Vortriebsrohren führte. Die benötigte Presskraft überstieg schlagartig die zulässige Belastbarkeit der Vortriebsrohre, so dass der Vortrieb eingestellt werden musste.
Einziger Lichtblick in diesem Drama war, dass die Vortriebsmaschine an der einzigen Stelle zum Liegen gekommen war, wo eine Bergung von Übertage aus möglich war. Nur in diesem Bereich lag der über der Trasse liegende Schmutzwasserkanal nicht direkt oberhalb des Vortriebes und die Trasse lag nicht im unmittelbaren Straßenbereich der Rue de Neudorf. Weder eine mögliche Vollsperrung noch ein Umpumpen/Umlegen des über der Maschine liegenden Schmutzwasserkanals wären möglich gewesen.
Auch so dauerte das Erstellen einer bis zu 8 m tiefen Bohrpfahlgrube seine Zeit, so dass der Vortrieb für die Dauer von rund 8 Monaten zum Erliegen kam. Diese Zeit wurde von allen Projektbeteiligten für eine intensive Diskussion genutzt. Einerseits natürlich, um zu ergründen, wie es zu dem Stillstand kam, und in einem zweiten Schritt, wie auf den verbleibenden Trassenabschnitten verhindert werden kann, dass ein solches Ereignis ein zweites Mal auftritt. Wie oben beschrieben: Auf dem gesamten verbleibenden Trassenabschnitt besteht keinerlei Möglichkeit, die Maschine außerplanmäßig zu bergen. Mit anderen Worten: Einen zweiten Stillstand durfte es nicht geben.
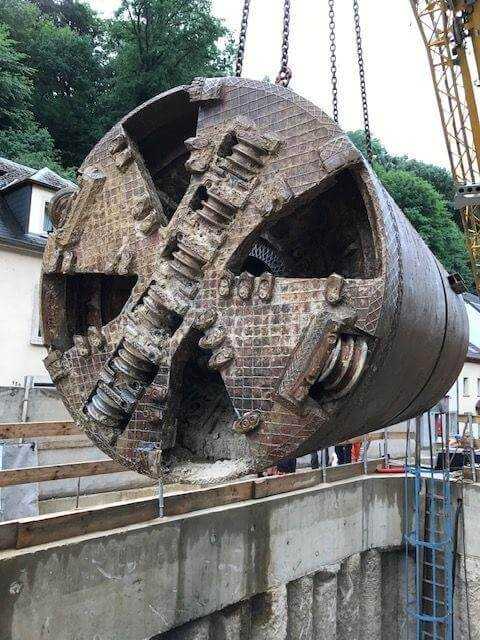
Diese Diskussion wurde mit sämtlichen Projektbeteiligten sehr intensiv und ergebnisoffen geführt. Zur Unterstützung der Firma Braumann wurde die Firma Babendererde Engineers beauftragt, sich aktiv an dieser Diskussion zu beteiligen.
Gemeinsam Lösungen erarbeitet
Die Ursache für den Stillstand konnte aufgrund des eindeutigen Schadensbildes der zwei betroffenen Rohre relativ schnell ermittelt werden. Aufgrund des in diesem Bereich sehr klüftigen Gesteins hatten sich oberhalb des Rohrfirstes Steine gelöst. Ein Teil dieser Steine wurde im Verlauf des weiteren Vortriebes in den Ringraum gezogen und hat sich dort aller Wahrscheinlichkeit nach derart verkeilt, dass eine immense Punktbelastung auf das darunter liegende Rohr ausgeübt wurde. Diese Punktbelastung führte dann zum Totalversagen zweier Rohre und zum Stillstand dieses Vortriebes.
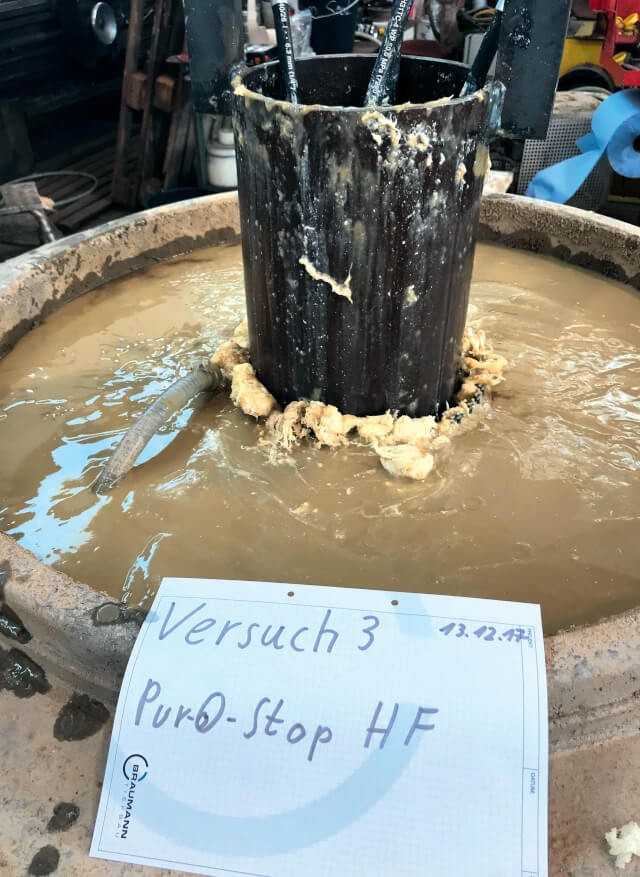
Nach Auswertung aller relevanten Vortriebsdaten fokussierte sich die Diskussion auf die Frage, wie der Ringspalt nachhaltig, sicher und vor allem vollständig für die gesamte Dauer der verbleibenden Vortriebe gefüllt werden kann. Darüber hinaus stellte sich die Frage, wie ein Auswaschen des Schmierfilmes, aufgrund des stark strömenden Grundwassers, sicher verhindert werden konnte.
Folgende Lösungen konnten dann gemeinsam mit dem Auftraggeber und den beteiligten Ingenieurbüros erarbeitet werden:
1. Inbetriebnahme einer zweiten, leistungsfähigen Bentonitschmieranlage, die ausschließlich als Kopfschmierung dient. Eine zweite Bentonitanlage übernimmt anschließend vollautomatisch die Strangschmierung.
2. Datenaufnahme und Protokollierung über eine zentrale Datenschnittstelle sowie Auswertung und graphische Aufarbeitung über das Datenmanagementsystem TPC der Babendererde Engineers.
3. Um zu verhindern, dass drückendes Grundwasser auf der gesamten Rohrlänge den schützenden Bentonitschmierfilm wegspült, wurde beschlossen, den Ringraum in vorher definierten Abständen durch sogenannte Schotts zu segmentieren. Da auf diesem Gebiet absolutes Neuland beschritten wurde, bestanden keinerlei Erfahrungswerte, wie diese Schotts aussehen könnten, noch aus welchem Material sie hergestellt werden könnten. Folgende Randbedingungen mussten erfüllten werden:
a) hochreaktives Material, welches mit vertretbarem Aufwand in den Ringraum injiziert werden kann
b) flexibel genug, um keinerlei Zwängungen im Rohrstrang zu verursachen; Kurvenfahrt muss möglich sein
c) gute Ablösbarkeit vom Rohrstrang nach Aushärten des Schotts
d) stabil genug, um den Reibkräften von über 300 m Vortrieb Stand zu halten
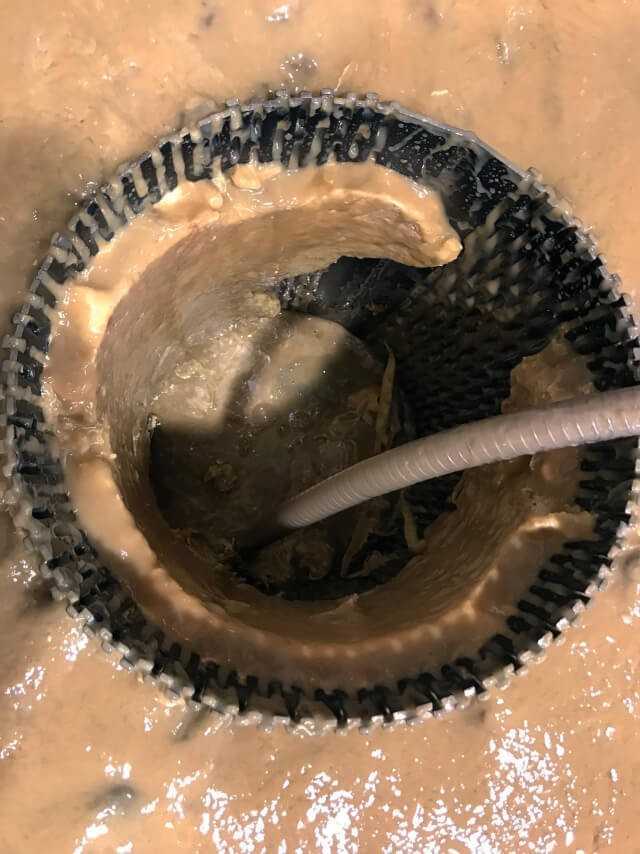
Versuche mit Acrylatgel und PU-Schaum
Nach intensiven Beratungen mit der Firma TPH Bausysteme legte sich der Fokus auf ein schnell reaktives Acrylatgel, welches die oben genannten Forderungen am besten abbildete. Um die theoretischen Werte möglichst praxisnah abzubilden, wurde beschlossen, das Gel in einem Versuchsaufbau zu testen. Bei diesem Versuch konnte das Einbringen des Gels in einem strömenden/fließenden Bentonitstrom simuliert werden. Außerdem konnte – nach erfolgter Schottsetzung – die benötigte Abreißkraft und die Schottausbildung gemessen werden.
Die Versuche mit dem Acrylatgel waren vollkommen unbefriedigend. Das Gel flockte in der Bentonitumgebung aus und zeigte keinerlei Neigung, sich zu einem homogenen Schott aufzubauen.
Als zweites Mittel wurde vom Hersteller ein Zweikomponenten-PU-Schaum vorgeschlagen. Gegen dieses Produkt bestanden von Seiten des AG und auch der Fa. Braumann gewisse Vorbehalte. Zum einen schäumt das Produkt um den Faktor 3 auf, so dass von Seiten des AG Sorgen bestanden, dass der Rohrstrang unzulässig gezwängt werden könne. Von Seiten der Fa. Braumann bestanden Bedenken, dass das frische Schott sich nicht an der Rohrwandung, sondern im inneren Gefüge ablöst.
Erstaunlicherweise konnten in den nachfolgenden Versuchen sämtliche Bedenken zerstreut werden. Das Material baute sich zu einem stabilen Schott auf und löste sich sauber von den Rohren. Auch die dafür notwendige Löseleistung war erfreulich niedrig, so dass einvernehmlich beschlossen wurde, das Produkt einzusetzen.
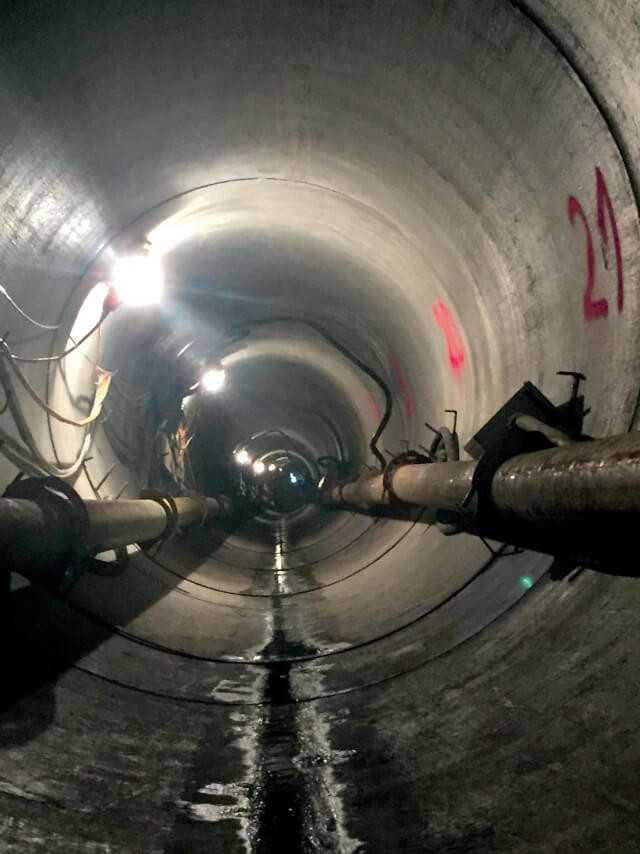
Gläserner Vortrieb
Um das Material möglichst punktgenau einzubringen und auch um humane Arbeitsbedingungen vor Ort zu schaffen, wurde ein sogenanntes Schottrohr gebaut. Dieses wurde unmittelbar hinter dem Nachlaufrohr der Vortriebsmaschine angeordnet. Jeweils ein Dehner vor und nach dem Schottrohr sorgten für die notwendigen Kraftreserven für den Fall, dass ein Schott doch einmal für höhere Abreißwerte sorgen sollte.
Die Fa. TPC ergänzte seine Software derart, dass auch die Schotts auf dem Computer visualisiert werden konnten. Absolut alle Messwerte des Vortriebes wurden dokumentiert, archiviert und grafisch aufbereitet, so dass man hier mit vollem Recht von einem gläsernen Vortrieb sprechen konnte. Sämtliche Vortriebsdaten wurden sowohl dem AG, den beteiligten Ingenieurbüros und der Fa. Braumann online und in Echtzeit zur Verfügung gestellt.

Erfolgreicher Abschluss
Derart gerüstet konnte der Vortrieb nach rund 8 Monaten Stillstand wieder aufgenommen werden. Die Grube, die zur außerplanmäßigen Bergung der Vortriebsmaschine notwendig wurde, konnte als Pressgrube genutzt werden und so begann am 21. März 2018 der Vortrieb der längsten Haltung dieser Baumaßnahme. Dieser Streckenabschnitt mit rund 370 m stellte sich von der Geologie sehr anspruchsvoll dar. Die verschiedenen Maßnahmen wie Schottsetzung, Bentonitkontrolle, Fugenvermessung usw. machten aber auch diesen Abschnitt beherrschbar und am 4. September 2018 konnte die Maschine erfolgreich geborgen werden.
Rohrpost abonnieren!
Wir graben für Sie nach Neuigkeiten. Die Ergebnisse gibt es bei uns im Newsletter.
Jetzt anmelden!
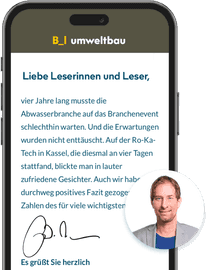
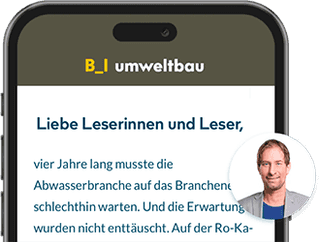
Fazit: Ein derart komplexer Vortrieb kann nur dann mit Erfolg aufgefahren werden, wenn von Anfang an sämtliche beteiligten Akteure an einem Strang ziehen und ihre jeweiligen Interessen dem Erfolg der Baustelle unterordnen. Dieses ist auf dieser Baustelle in Luxemburg vorbildlich gelungen.
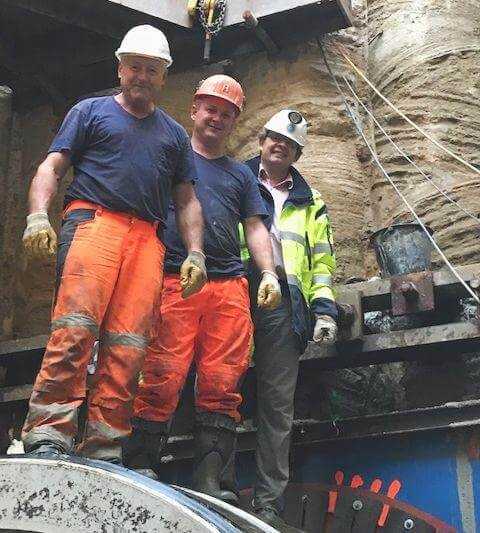
Weiterlesen:
Neueste Beiträge:
Meistgelesene Artikel
Für welche Leistungsart interessieren Sie sich?
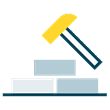
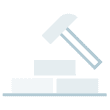
Bauleistungen
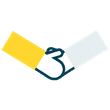
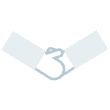
Dienstleistungen
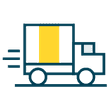
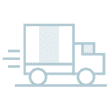
Lieferleistungen
Top Bau-Themen:
Aktuelle Termine für unterirdische Infrastruktur
25.08.2025 - 26.08.2025
Seminar Bedarfsorientierte Kanalreinigung10.09.2025
Norddeutsche KanalsanierungstageJetzt zum Newsletter anmelden:
Leitungsbau, Kanalsanierung, Abwasser – erfahren Sie das wichtigste rund ums Thema unterirdische Infrastruktur.