Cable & Pipe: Oberflächennahe Verlegung von Kabelschutzrohren
Cable & Pipe (C&P) ist ein neues modifiziertes HDD-Verfahren, mit dem Kabelschutz- und Produktrohre oberflächennah verlegt werden können, ohne dass es zu ohne Spülungsausbrüchen kommt.
In den letzten fünf Jahren hat es im HDD-Markt in Deutschland eine signifikante Verschiebung der Tätigkeitsschwerpunkte gegeben. Immer mehr Kapazitäten und Know-how werden für die Verlegung von Kabelschutzrohren für Energie- und Datenkabel eingesetzt, während gleichzeitig die Verlegung von Rohrleitungen für den Gas- und Wassertransport stagniert, eventuell sogar rückläufig ist.
Von dieser Entwicklung waren im Bereich der Bohranlagen nicht nur die Mini- und Midi-Bohranlagen betroffen, sondern auch für Maxi- und Mega-Bohranlagen ergaben sich neue Projekte mit Bohrungslängen von über 1 km, teilweise auszuführen in sehr schwierigen Geologien oder in ökologisch besonders sensiblen Bereichen wie z.B. dem Wattenmeer. Während die kleineren Bohranlagen schwerpunktmäßig bei der Verlegung von Schutzrohren für Datenkabel (insbesondere Glasfaserkabel) eingesetzt wurden und werden, kommen viele der größeren Bohranlagen besonders auf den Trassen der Energiekabel zum Einsatz.
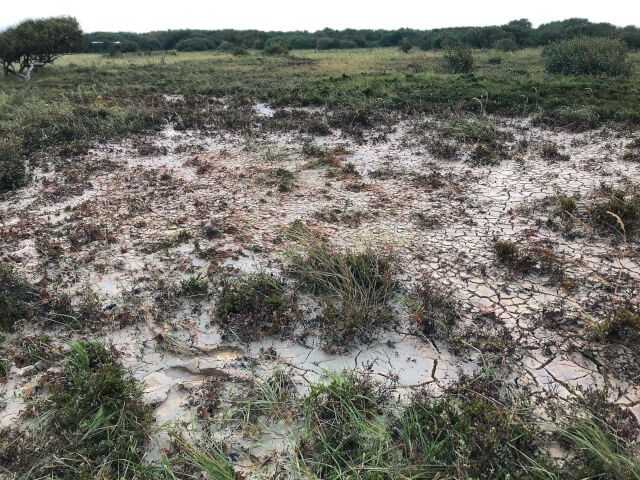
Besonderheiten der Energiekabelverlegung
Die für Energiekabel genutzten Kabelschutzrohre werden in der Regel aus dem Material Polyethylen hergestellt. Die Verlegung solcher Kabelschutzrohre mittels HDD-Verfahren stellt grundsätzlich zunächst keine anderen Anforderungen an die HDD-Verfahrenstechnik als bei Projekten für die Gas- und Wasserindustrie. Generell müssen bei PE-Rohren besonders die Belastungen durch den Beuldruck (sowohl während des Baus als auch während der späteren Betriebsphase) sowie die beim Rohreinzug in das Bohrloch auftretenden Zugkräfte beachtet werden.
Anders als bei den „konventionellen“ Projekten wird bei der Verlegung von Energiekabeln seitens der Energieversorger bzw. Kabelbetreiber aber eine möglichst flache Verlegung im Boden angestrebt. Diese Vorgabe hängt primär mit der Wärmeentwicklung und Wärmeabgabe der Kabel während der späteren Betriebsphase zusammen. Vereinfacht ausgedrückt gilt: Je tiefer ein Kabel im Boden verlegt wird, desto schlechter ist dessen Wärmeabgabe in den umgebenden Boden und desto größer werden die temperaturbedingten Leistungseinbußen.
Idealerweise sollte ein Energiekabel auch bei der Verlegung mittels HDD in einer Tiefenlage entsprechend derjenigen der offenen Verlegung installiert werden, d.h. ca. 1,5 bis 2,0 m unter Geländeoberkante. Dies ist jedoch beim „normalen“ HDD-Verfahren in der Regel nicht möglich, da der Druck der im Bohrloch zurückfließenden Bohrflüssigkeit in einem solchen Fall schnell größer würde als derjenige Druck, den der überlagernde Boden aushalten kann, ohne dass es zu Spülungsausbrüchen an der Geländeoberfläche kommt (Abb. 1).
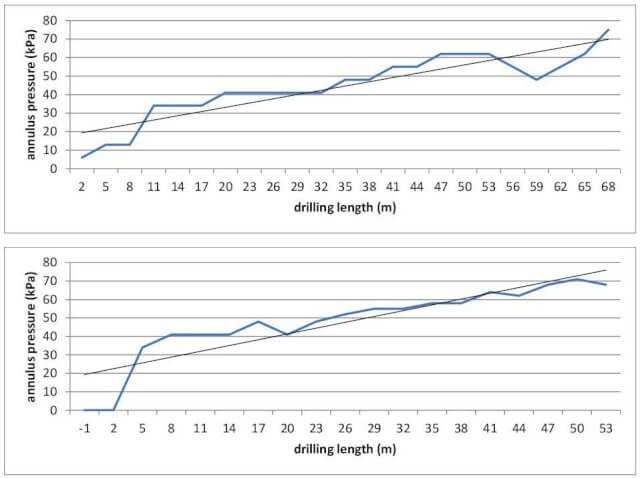
Hier gab es somit einen „Zielkonflikt“ zwischen den Wünschen der Energieversorger und Kabelbetreiber auf der einen Seite (möglichst niedrige Verlegetiefe, d.h. ca. 1,5 bis 2,0 m) und den Bohrfirmen auf der anderen Seite (möglichst „normale“ Verlegetiefe, d.h. ca. 10 bis 20 m).
Die oben gemachten Angaben zur Tiefenlage beziehen sich zunächst auf Projekte „auf der grünen Wiese“, d.h. Trassenabschnitte, auf denen eine offene Verlegung aus verschiedenen Gründen (z.B. Umweltschutz) nicht oder nur stark eingeschränkt möglich ist. Sie gelten im Prinzip aber auch für typische HDD-Projekte, wo z.B. ein Gewässer unterquert werden muss. Auch hier besteht seitens der Energieversorger und Kabelbetreiber der Wunsch nach möglichst geringer Überdeckung im Gewässerbereich, um auch in den auf- und absteigenden Teilen der Bohrung möglichst geringe Bodenüberdeckungen realisieren zu können.
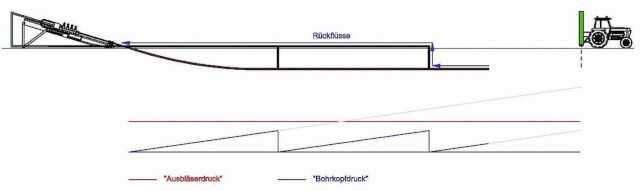
Motivation für ein neues Verfahren
Geringe Bodenüberdeckungen – unabhängig davon, ob unter einer ebenen Fläche oder einem Gewässer – sind zwar prinzipiell mit dem HDD-Verfahren realisierbar, bergen aber fast immer (abhängig vom Boden) ein großes Potenzial für Spülungsausbrüche. Insofern musste „nur“ ein Weg gefunden werden, das Spülungsausbruchrisiko – insbesondere während der Pilotbohrung – zu eliminieren, um den Wünschen der Energieversorger und Übertragungsnetzbetreiber entgegenzukommen.
Die wesentliche Zielsetzung für ein neues Verfahren bestand also darin, den Spülungskreislauf so zu optimieren, dass der im Ringraum entstehende Druck der Bohrflüssigkeit auch bei sehr langen Bohrungen immer niedriger als der zulässige Ringraumdruck bleiben würde. Gleichzeitig sollte aber auch die Forderung erfüllt werden, alle anderen Elemente des bekannten HDD-Verfahrens möglichst beizubehalten, um großen Investitionen in Geräte und die Ausbildung der Bohrmannschaften zu vermeiden und dadurch zu einem wirtschaftlich konkurrenzfähigen Verfahren zu gelangen. Mit anderen Worten: Die gegenüber dem konventionellen HDD-Verfahren zu erwartenden Mehrkosten sollten für ein neues Verfahren maximal etwa 10% betragen.
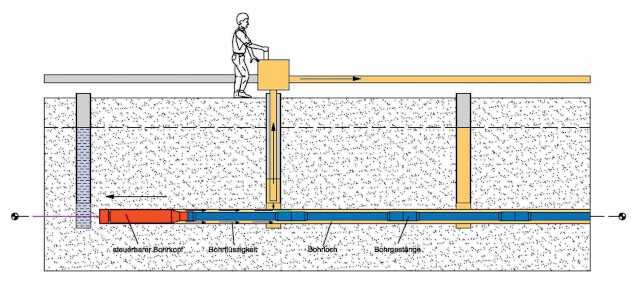
Theoretische Betrachtung des Ringraumdrucks
Der dynamische Druck beschreibt denjenigen Druck, der erforderlich ist, die mit Bohrklein beladene Bohrflüssigkeit durch den Ringraum zwischen Bohrlochwand und Bohrgestänge in Richtung Eintrittspunkt zu drücken. Dieser dynamische Druck wird von mehreren geometrischen und rheologischen Faktoren beeinflusst, z.B. von
- Bohrungslänge
- Bohrlochdurchmesser
- Bohrgestängedurchmesser
- Pumprate
- plastischer Viskosität
- Fließgrenze.
Die Berechnung des dynamischen Drucks ist möglich, wenn die oben genannten Parameter genau bekannt sind, also für theoretische Betrachtungen und Abschätzungen. In der Praxis lässt sich aber eine exakte Vorhersage oder Einstellung des dynamischen Drucks nicht umsetzen, da es besonders im Bereich der Eigenschaften der Bohrflüssigkeit zu viele unbekannte Parameter und Veränderungen gibt.
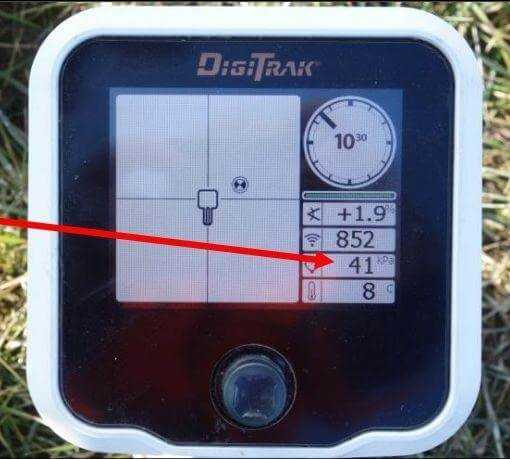
Praxiswerte zum dynamischen Druck im Ringraum
Durch Feldversuche und genaue Drucküberwachungen der Pilotbohrungen von konventionellen HDD-Projekten hat sich gezeigt, dass der dynamische Druck sich in relativ engen Grenzen bewegt, und zwar zwischen etwa 0,3 und etwa 0,7 bar pro 100 m Bohrungslänge (Abb. 2). Der niedrigere Druck wird eher in Pilotbohrungen mit relativ großem Bohrkopfdurchmesser und/oder relativ niedrigviskoser Bohrflüssigkeit erreicht, der höhere dynamische Druck demgegenüber eher in Pilotbohrungen mit relativ kleinem Bohrkopfdurchmesser und/oder relativ hochviskoser Bohrflüssigkeit.
Nicht berücksichtigt werden können bei diesen Abschätzungen andere Einflussfaktoren, wie z.B.
- Bohrlocheinstürze in Teilbereichen der Bohrung (z.B. in Kies)
- Bohrkleinsedimentation im Bohrkanal
- Querschnittsverengungen durch quellende Formationen (z.B. Ton)
Der Fracture Gradient
Unter dem Fracture Gradient (auch Frac-Gradient genannt) wird in der Tiefbohrtechnik derjenige Bohrlochdruck verstanden, bei dem eine bestimmte Formation „bricht“. Auch in der Tiefbohrtechnik wird dieser Druck genutzt, um die maximal zulässigen Bohrlochdrücke zu berechnen bzw. abzuschätzen. Hierbei liegt der Fokus jedoch ganz klar auf Festgesteinsformationen und sehr großen Bohrungstiefen. Als Einheit wird dabei in der Ölbohrtechnik in der Regel „psi/ft“ genutzt, für die Anwendung in der HDD-Technik in Deutschland hat sich als Einheit „bar/m“ als sinnvoll erwiesen.
Für die hier betrachtete Anwendung auf oberflächennahe HDD-Bohrungen in Lockergesteinen können die Kennwerte für felsige Formationen nicht genutzt werden. Wie schon für den dynamischen Druck gilt auch für den Frac-Gradient von Lockergesteinen, dass sich dieser zwar theoretisch berechnen lässt, wenn alle erforderlichen bodenspezifischen Kennwerte vorhanden sind, in der Praxis wird eine derart umfangreiche Bodenerkundung aber im Prinzip nie durchgeführt. Aus diesem Grund müssen auch hier wieder Richtwerte genutzt werden, die aus diversen Versuchen und Projekten generiert wurden. Für einige häufige Bodenarten können folgende Richtwerte (!) angenommen werden:
- Grobkies => ca. 0,1 - 0,5 bar/m
- Mittelkies => ca. 0,2 - 0,6 bar/m
- Feinkies => ca. 0,3 - 0,7 bar/m
- Grobsand => ca. 0,4 - 0,8 bar/m
- Mittelsand => ca. 0,5 - 0,9 bar/m
- Feinsand => ca. 0,6 - 1,0 bar/m
- Schluff => ca. 0,7 - 1.1 bar/m
- Ton => ca. 0,8 - 1,2 bar/m
Es ist zu beachten, dass die aufgeführten Richtwerte großen Schwankungsbreiten unterliegen, z.B. aufgrund der Kornform, der Lagerungsdichte, der Klüftigkeit, dem Quellvermögen etc., und im Einzelfall von den obigen Werten abweichen können. Diese Richtwerte müssen deshalb noch durch weitere Praxiserfahrungen verifiziert werden, sie sind aber jetzt schon bei der Planung von C&P-Projekten von großem Nutzen.
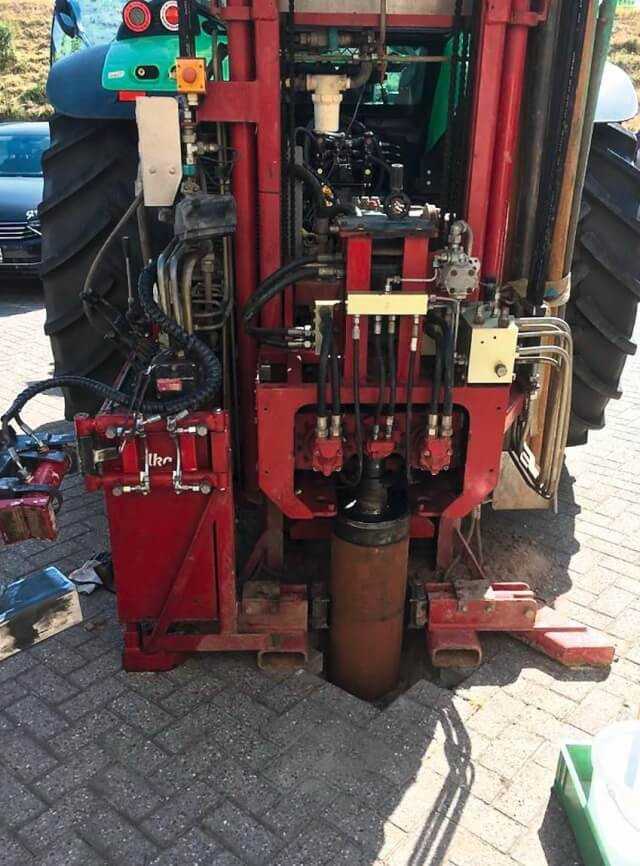
Das C&P-Verfahren
Der Grundgedanke des C&P-Verfahrens besteht darin, den Spülungskreislauf vorsätzlich „kurzzuschließen“, indem von der Oberfläche in geeigneten Abständen (abhängig vom anstehenden Boden und der geplanten Tiefenlage) Vertikalbohrungen niedergebracht und diese über ein Pumpen- und Leitungssystem mit der Ein- bzw. Austrittsgrube verbunden werden (Abb. 3).
Dadurch soll der Weg, den die mit Bohrklein beladene Bohrflüssigkeit durch den Ringraum zurücklegen muss, stark eingekürzt werden, wodurch gleichzeitig der dynamische Druckanteil signifikant absinkt. Durch das geeignete Positionieren der Vertikalbohrungen – abhängig von der Tiefenlage der Pilotbohrung und dem Frac-Gradienten des Bodens – können so sehr lange Pilotbohrungen oberflächennah durchgeführt werden, ohne an der Geländeoberfläche zu Spülungsausbrüchen zu führen (Abb. 4).
Beispiel:
Bohrungslänge => 1.500 m
Tiefenlage => 3 m
Baugrund => Mittelsand
Abstand der Vertikalbohrungen => ca. 300 m
Theoretische Anzahl an Vertikalbohrungen => ca. 5 Stück
Aufgrund der geringen Tiefenlage der Pilotbohrung ist es beim C&P-Verfahren durchaus vorstellbar, die Vermessung mittels Walk-Over-System durchzuführen und dadurch Zeit- und Kostenvorteile gegenüber dem bei sehr langen Bohrungen üblichen Wireline-Verfahren zu generieren. Dies umso mehr, als in modernen Walk-Over-Vermessungssystemen mittlerweile auch ein Drucksensor integriert wurde, mit dem der exakte Ringraumdruck am Bohrkopf kontinuierlich überwacht werden kann (Abb. 5).
Multifunktionsbohrungen (MFB)
Die beschriebenen Vertikalbohrungen werden beim C&P-Verfahren jedoch nicht nur für die Veränderung des Spülungskreislaufs genutzt, sondern liefern auch wertvolle „Erste-Hand“-Informationen zum tatsächlich anstehenden Baugrund. So konnten in der Praxis schon Geröll- und Tonschichten erkannt werden, die im „normalen“ Baugrundgutachten nicht verzeichnet waren. Dadurch war es möglich, die Bohrspülung für diesen Abschnitt zu optimieren und die bohrtechnischen Beobachtungen (z.B. hohe Drehmomente) richtig zuzuordnen. Die Vertikalbohrungen können außerdem genutzt werden, um nach dem Einzug des Schutzrohrs den verbleibenden Ringraum abschnittsweise „von oben“ zu verdämmen und dabei gleichzeitig die verdrängte Bohrspülung über die benachbarten Vertikalbohrungen und durch die vorhandene Rohrleitung abzufördern. Wegen der Möglichkeit der Mehrfachnutzung der Vertikalbohrungen hat sich in der Praxis der Begriff „Multifunktionsbohrung“ (MFB) für diese Vertikalbohrungen durchgesetzt. Das Abteufen dieser MFB wird je nach Tiefenlage der Pilotbohrung mittels Anbauschnecke und kleinem Bagger oder als Anbauvorrichtung an einen normalen Traktor mit Standard-Dreipunktaufhängung und Hydraulikanschlüssen durchgeführt (Abb. 6).
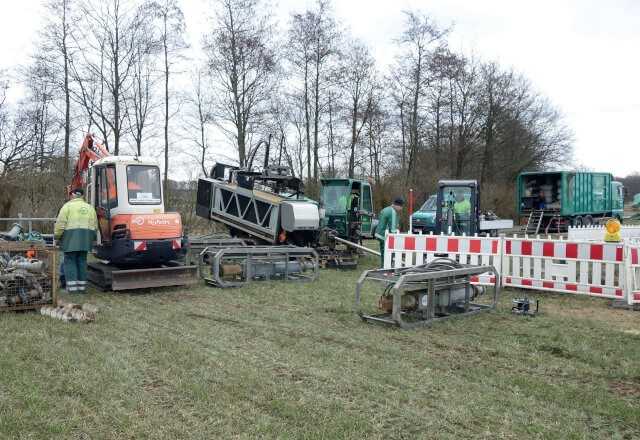
Feldversuch an der Ems
Die Firmen Beermann Bohrtechnik GmbH aus Riesenbeck und Bohlen & Doyen GmbH aus Wiesmoor haben die praxisreife Entwicklung des von Dr. Kögler aus Uplengen-Nordgeorgsfehn konzipierten und inzwischen europaweit für die beiden genannten Bohrfirmen patentierten C&P-Verfahrens in die Tat umgesetzt. Dazu wurde in einem ersten Schritt im März 2018 ein Feldversuch im Emsland durchgeführt, bei dem mehrere Testbohrungen von jeweils ca. 50 – 100 m in nur 1 bis 1,2 m Tiefe in sehr dicht gelagertem Sand durchgeführt wurden (Abb. 7).
Alle Testbohrungen konnten die theoretischen Vorhersagen vollumfänglich bestätigen. Dadurch konnte in der Praxis ein erster Nachweis dafür erbracht werden, dass mit C&P tatsächlich oberflächennahe Horizontalbohrungen ohne Spülungsausbrüche an der Geländeoberfläche durchgeführt werden können. Die Testbohrungen wurden vom Ingenieurbüro Dr. Veenker aus Hannover unabhängig und objektiv begleitet, dokumentiert und ausgewertet. Neben den genannten Firmen und Personen wurde dieses Testprojekt von vielen geladenen Gästen aus der Industrie (Ingenieurbüros, Kabelbetreiber, Energieversorger etc.) mit großem Interesse vor Ort verfolgt.
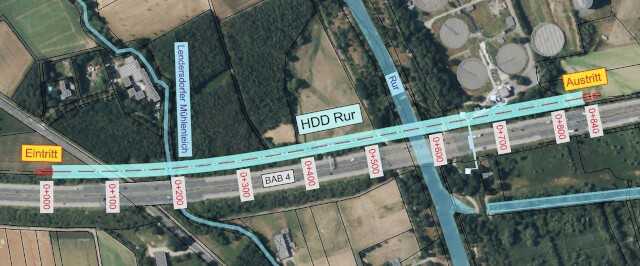
Ersteinsatz auf der ALEGrO-Trasse
Nachfolgend wird beispielhaft die Realisierung des größeren C&P-Projekts auf der ALEGrO-Trasse – die Unterquerung der Rur bei Düren – näher beschrieben.

Unterquerung der Rur
Neben dem Kernparameter (Braunkohlenschicht) gab es noch einige weitere technische Herausforderungen bei diesem Projekt zu bewältigen. Nicht alle dieser Herausforderungen waren vor Bohrungsbeginn bekannt und mussten deshalb vor Ort in enger Koordination und Kooperation zwischen Bohrfirma, Bauherr und Ingenieurbüro gelöst werden. Einige dieser Herausforderungen sind nachstehend kurz aufgeführt:
- eine horizontale Kurve im Eintrittsbereich
- sehr enge Vorgaben hinsichtlich der horizontalen Lage der Bohrungen (teilweise unter einem öffentlichen Weg)
- sandig-kiesig-toniger Mischboden mit nicht genau bekannten Grenzen
- massive Störungszone etwa in der Mitte der Bohrstrecke (genaue Lage vorab unbekannt)
- kreuzende Fremdleitungen, teilweise nicht in den aktuellen Bestandsplänen verzeichnet
- über weite Streckenabschnitte parallel verlaufende Abwasserleitung
- ein weiteres zu unterbohrendes Gewässer mit hoher Fließgeschwindigkeit (Lendersdorfer Mühlenteich)
- eine zu unterquerende Bundesstraße mit dazu parallel verlaufenden Fremdleitungen nach ca. 80 m Bohrstrecke
- eine massive Kiesschicht im Eintrittsbereich (kompletter Bodenaustausch erforderlich)
- ein sehr harter Tonabschnitt zwischen der Störung und der Rur (vorab nicht bekannt)
- teilweise schwierige Topographie und Zugänglichkeit, insbesondere im letzten Abschnitt der Bohrung
- Schutzrohre mussten wegen zu kurzer Rohrbaufläche jeweils mit einer Garantienaht hergestellt werden (dadurch notwendigerweise Unterbrechung der jeweiligen Einziehvorgänge).
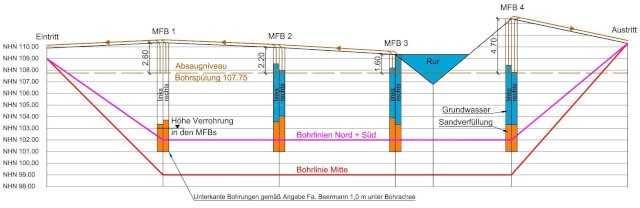
Tab. 1: Wichtige Kennwerte der drei Bohrungen unter der Rur
Parameter Energiekabel 1 Begleitkabel Energiekabel 2
Schutzrohrdimension 280 mm x 31,2 mm 280 mm x 31,2 mm 280 mm x 31,2 mm
Schutzrohrmaterial PE 100 PE 100 PE 100
Länge 832 m 846 m 833 m
Max. Tiefenlage 101 mNN 98 mNN 101 m
Überdeckung Rur 4,5 m 7,5 m 4,5 m
Bohrlochdurchmesser 480 mm 480 mm 480 mm
Bohrlochvolumen 150 m3 153 m3 150 m3
Eintrittswinkel 11° 10° 10°
Austrittswinkel 8° 8° 8°
Radius horizontal 1.600 m 1.600 m 1.600 m
Radius vertikal 400 m 400 m 400 m
Radius kombiniert 388 m 388 m 388 m
Planung und Bau der MFB
Basierend auf den vor Bohrungsbeginn bekannten Parametern wurden zunächst die genauen Bohrlinien für die drei Bohrungen optimiert. Dann wurden mit Hilfe des bekannten Programms „D-Geo Pipeline“ die zu erwartenden Ringraumdrücke, Zugkräfte, Materialspannungen etc. berechnet. Schnell wurde klar, dass bei Einsatz eines konventionellen HDD-Verfahrens die Wahrscheinlichkeit von Spülungsausbrüchen unvertretbar hoch sein würde (Abb. 9) und deshalb das C&P-Verfahren zur Anwendung gelangen sollte.
In enger Abstimmung mit den beteiligten Parteien und unter Hinzuziehung von Dr. Kögler als Berater des Bauherrn wurden gemeinsam die Anzahl und die besten Positionen der abzuteufenden Multifunktionsbohrungen festgelegt (Abb. 10). Anschließend wurden die Details der MFB (Tiefe, Verrohrung, Durchmesser etc.) bestimmt und geeignete Maschinentechnik ausgewählt, um die teilweise sehr großen Bohrungstiefen (bis ca. 10 m) zu erreichen.
Eine geringere Tiefenlage als bei ca. 102 mNN war aufgrund der bis ca. 4 m unter GOK (d.h. bis ca. 106 mNN) anstehenden Kiesschicht mit Steinen und Blöcken sowie dem Flussbett der Rur (bei ca. 106 mNN) nicht sinnvoll. Die Bohrlinienplanung war somit nach oben durch den Kies und nach unten durch die Braunkohleschicht eingeengt.
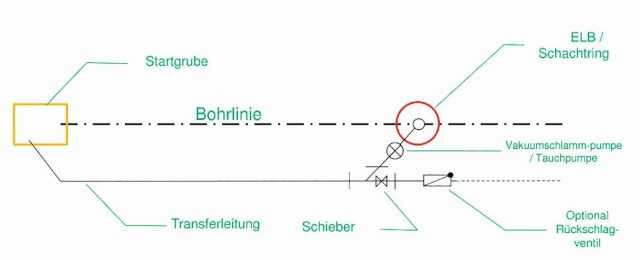
Pumpen und Rückspülleitung
Einen wichtigen Beitrag zum Gelingen des C&P-Verfahrens musste neben den beschriebenen MFB auch das zugehörige Pumpen- und Leitungssystem erbringen (Abb. 11). Dazu war es zunächst erforderlich, die Bauart, die Förderleistung und den Förderdruck der Pumpen auf die projektspezifischen Bedingungen wie z.B. Straßenüberquerungen abzustimmen.
Betrieb der MFB
Das Konzept für die Anordnung und Ausgestaltung der MFB und der Rückspülleitung hat sich insgesamt sehr gut in der Praxis bewährt (Abb. 12). Insbesondere die MFB-3 direkt vor der Rur hat sich als „Match Winner“ erwiesen, da hier noch einmal deutlich der Ringraumdruck gesenkt werden konnte, bevor der Bohrkopf mit sehr geringer Deckung plangemäß unter der Rur hindurchgeführt wurde.
Allerdings gab es auch einige Besonderheiten bei diesem Erstprojekt zu beobachten. Zunächst konnte festgestellt werden, dass geringfügige Überschreitungen des vorgegebenen Maximaldrucks (2,2 bar im „normalen“ Teil der Bohrung, 1,8 bar unter der Rur) zu keinen Spülungsausbrüchen führten und deshalb die angenommenen Frac-Gradienten als konservative Werte anzusehen sind.
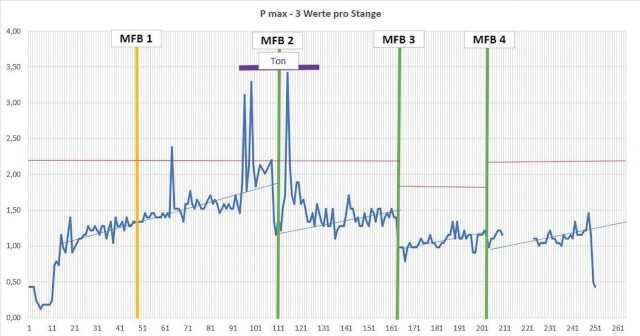
Des Weiteren wurde keine der beiden MFB am ersten Standort in ca. 150 m vom Eintrittspunkt entfernt zu irgendeinem Zeitpunkt der Projektdurchführung aktiv. Der Grund hierfür ist nicht eindeutig zu verifizieren. Es könnte sowohl mit der Erstellung der beiden MFB zusammenhängen (z.B. zu starke Verdichtung des untersten Teils) oder mit dem Umstand, dass der tatsächlich entstehende dynamische Druck für den Spülungstransport bis zum Eintrittspunkt mit ca. 0,35 bar einfach zu gering war, um die (planungskonforme) Verfüllung der MFB zu brechen.
Diese letzte Möglichkeit deutet bereits auf eine weitere Besonderheit dieser Bohrung hin: Der erforderliche dynamische Druck im Ringraum war mit ca. 0,25 bar pro 100 m an der Untergrenze der theoretischen Vorhersagen. Im Rückblick lässt sich somit schlussfolgern, dass man mit einer mutigeren Annahme hinsichtlich des dynamischen Drucks (statt 0,50 bar zum Beispiel nur 0,30 bar pro 100 m) auf zwei der insgesamt vier MFB-Standorte sogar hätte verzichten können (und zwar den ersten und den letzten Standort). Eventuell wäre es sogar möglich gewesen (zumindest, wenn es im Bereich der Rur keinen Geländeeinschnitt gegeben hätte), durch Verschiebung bzw. Zusammenführung der Standorte 2 und 3 nur an einer einzigen Position MFB zu installieren. Bei einer mittleren Geländeüberdeckung von ca. 8 m wäre dann nur eine MFB alle 400 m erforderlich. Umgerechnet auf die von den Kabelherstellern angestrebte Tiefenlage von z.B. 2 m würde dies etwa einen MFB-Standort alle 100 m erfordern (mit MFB-Tiefen von nur ca. 2 m).
Eine weitere Besonderheit bei diesem Projekt war die außergewöhnlich wichtige Funktion am dritten Standort vor der Rur. In diesem Bereich mussten sich die Pilotbohrungen durch extrem harten und teilweise zum Quellen neigenden Ton kämpfen. Trotz mehrfacher Anpassung der Bohrspülung durch die anerkannte Fachfirma Phrikolat GmbH aus Hennef gelang es einfach nicht, die beim Bohrvorgang entstehenden Tonkörper aus dem Bohrloch zu befördern und Druckspitzen oberhalb der geplanten Maximalwerte gänzlich zu vermeiden. Selbst Transportlängen von 10 – 20 m führten sehr schnell zum kompletten Verstopfen des Ringraums. Gelöst werden konnte dieses Problem nur durch sehr häufiges Zurückziehen des Bohrkopfs (bis sich wieder Rückfluss einstellte). Allerdings erforderte es schon größte Anstrengungen, diese Rückflüsse alleine bis zur MFB-3 herzustellen. Ohne diese MFB wäre es sehr wahrscheinlich gar nicht möglich gewesen, den Ringraum von den Ton-Cuttings zu befreien. Aber selbst in den kurzen Steigrohren der MFB-3 kam es immer wieder zu Tonstopfen, die mühsam mechanisch beseitigt werden mussten.
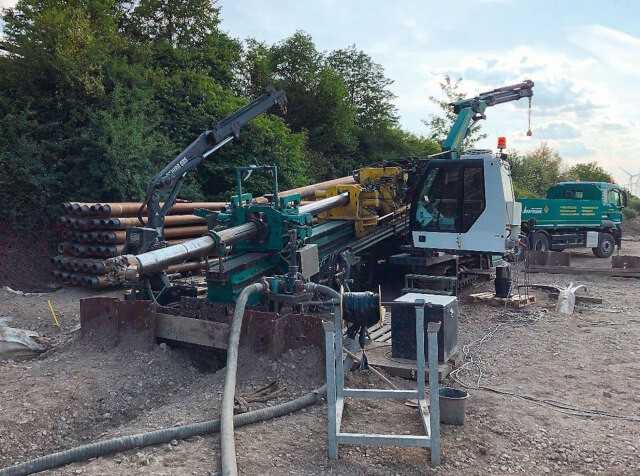
Bohrungsdurchführung
Im Rahmen der Baugrunderkundung wurden im Eintrittsbereich die schwierig bohrbaren Rurkiese in Tiefen bis ca. 4,8 m erkundet, die regelmäßig grobkiesig und steinig sind und auch Blöcke enthalten. Aus diesem Grund wurde entschieden, in diesem Bereich einen umfangreichern Bodenaustausch vorzunehmen. Als Austauschboden wurde wie bereits bei anderen Projekten zeitweise fließfähiger Verfüllbaustoff (ZFSV) gewählt, der sich bei der späteren Bohrtätigkeit gut bohrbar und ausreichend stabil zeigte.
Alle Bohrungen wurden alle drei Einzelbohrungen mit der 100-t-Bohranlage von Beermann mit 6.5/8“ Bohrgestänge durchgeführt (Abb. 13). Dabei wurde für die Pilotbohrung ein 12.1/4“-Rollenmeißel in Kombination mit einem Gyro-Messsystem eingesetzt. Anschließend wurde die Pilotbohrung auf einen Durchmesser von 480 mm mittels Barrel Reamer aufgeweitet, bevor im letzten Arbeitsschritt die PE-Rohre 280 x 31,2 mm eingezogen wurden. Der Ziehkopf wies dabei jeweils Öffnungen auf, so dass die PE-Rohre innen mit Bohrflüssigkeit gefüllt waren und so nur geringen Auftrieb im Bohrloch aufwiesen.
Die schwierigsten Arbeitsschritte aller drei Bohrungen waren die drei Pilotbohrungen, da sowohl die Steuerbarkeit (z.B. im Bereich der Störung) als auch der Bohrkleintransport in der Tonschicht (s.o.) einige Probleme bereiteten, letztendlich aber beherrscht werden konnten. Ebenso waren auch die Stillstandszeiten bei den Einziehvorgängen während der Herstellung der Garantienähte (Stillstand jeweils ca. 2 Stunden) unkritisch, da nach der Weiterführung der Einziehvorgänge weder besondere Anstiege bei der Zugkraft noch beim Drehmoment festzustellen waren (Abb. 14).
Größere Probleme bereitete da schon die Kiesschicht im Austrittsbereich der drei Bohrungen. Hier wurden Bedingungen angetroffen (Steine, Blöcke), die ein kontrolliertes Steuern des Pilotbohrkopf nicht mehr zuließen und deshalb dieser Bereich jeweils aufgegraben werden musste.
Die wichtigsten technischen Parameter der drei C&P-Bohrungen unter der Rur sind im Überblick in Tab. 2 zusammengefasst.
Tab. 2: Wichtige Kennwerte der drei Einzelbohrungen
Parameter Energiekabel 1 Begleitkabel Energiekabel 2
Bohranlage PD 100/50 RP PD 100/50 RP PD 100/50 RP
Bohrgestänge 6.5/8“ 6.5/8“ 6.5/8“
Bohrkopf 12.1/4“ 12.1/4“ 12.1/4“
Vermessungssystem Gyro Gyro Gyro
Dauer Pilot 5 Tage 4 Tage 5 Tage
Druckkräfte Pilot 50 – 100 kN 60 – 110 kN 40 – 160 kN
Drehmomente Pilot 15 – 25 kNm 5 – 26 kNm 8 – 28 kNm
Dauer Räumen 3 Tage 3 Tage 2 Tage
Zugkräfte Räumen 30 – 60 kN 15 – 20 kN 15 – 30 kNm
Drehmomente Räumen 20 – 30 kNm 10 – 28 kNm 15 – 30 kNm
Dauer Einziehen 1 Tag 1 Tag 1 Tag
Zugkräfte Einziehen 70 – 120 kN 190 – 220 kN 170 – 200 kN
Drehmomente Einziehen 10 – 30 kNm 10 – 31 kNm 8 – 30 kNm
Aktive MFBs 2, 3 und 4 2 und 3 2 und 3
Gesamtbohrzeit inkl.
Rohreinzug 9 Tage 8 Tage 8 Tage
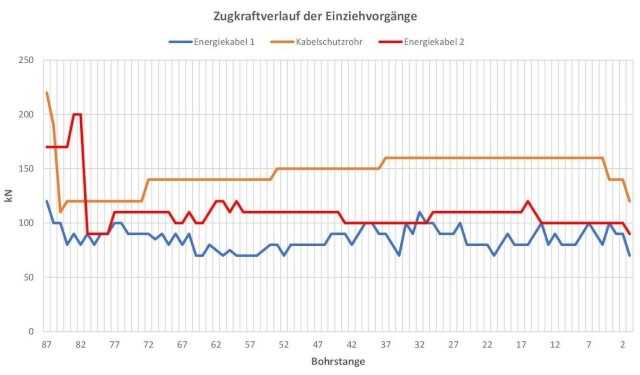
Wichtige Erfahrungen
Obwohl dieses erste größere C&P-Projekt keinesfalls idealtypisch für die neue Verfahrensweise war (da die Überdeckung mit 4 – 8 m deutlich höher war als die vorgesehenen 2 – 4 m), konnten dennoch folgende erste Erfahrungen gesammelt werden:
- Der dynamische Druckverlust im Ringraum liegt zumindest für die hier verwendete Bohrgarnitur bei nur 0,25 - 0,30 bar pro 100 m.
- Der Fließwiderstand im Boden (Frac-Gradient) kann für den angetroffenen Mischboden etwa mit ca. 0,50 - 0,60 bar pro Meter angesetzt werden.
- Der Abstand der Multifunktionsbohrungen kann zukünftig etwas progressiver angesetzt werden mit ca. 50 m Abstand je Meter Bodenüberdeckung.
- Erstellung und Betrieb der Multifunktionsbohrungen sowie das Pumpen- und Rückleitungsregime haben sich grundsätzlich bewährt. Bei geringeren Tiefenlage sollte aber aus wirtschaftlichen Gründen eine einfachere Bohrausrüstung (siehe Abb. 6) zum Einsatz gelangen.
- In tonigen Böden sollte ggf. der Durchmesser der Multifunktionsbohrungen vergrößert werden.
Ausblick
In einem nächsten Schritt sollte nun versucht werden, für das C&P-Verfahren ein Projekt zu finden, bei dem die angestrebte Tiefenlage von 2 – 4 m bei einer Bohrungslänge von 500 – 1.500 m realisiert werden kann. Je nach gefordertem Genauigkeitsgrad könnte dabei eventuell mit einem Walk-Over-System gebohrt werden, was sich ebenso positiv auf die Wirtschaftlichkeit auswirken könnte wie der Einsatz einer einfacheren Bohrausrüstung zum Abteufen der nur ca. 1,5 – 3,5 m tiefen Multifunktionsbohrungen.
Zusammenfassung
Bei dem ersten größeren Cable & Pipe-Projekt auf der ALEGrO-Trasse der Amprion GmbH hat sich dieses modifizierte HDD-Verfahren trotz sehr schwieriger Rahmenbedingungen hervorragend bewährt. Die dort gewonnenen Erkenntnisse werden schon bei den nächsten C&P-Projekten eine weitere Optimierung der Technik sowie eine Verbesserung der Wirtschaftlichkeit ermöglichen. Damit wird der Industrie ein weiteres „Werkzeug“ für die grabenlose Verlegung von Rohrleitungen zur Verfügung gestellt, das anwendungstechnisch zwischen dem klassischen HDD-Verfahren und der offenen Verlegung angesiedelt ist – sowohl technisch als auch wirtschaftlich.
Rohrpost abonnieren!
Wir graben für Sie nach Neuigkeiten. Die Ergebnisse gibt es bei uns im Newsletter.
Jetzt anmelden!
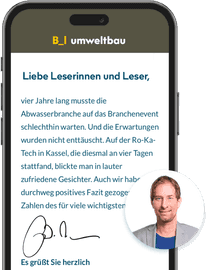
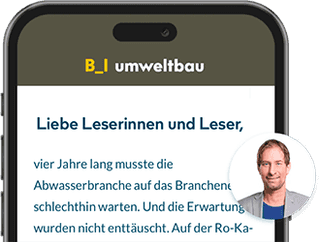
*Autoren:
Priv.-Doz. Dr.-Ing. habil. Rüdiger Kögler, Sworn Expert HDD/ö.b.u.v. Sachverständiger für HDD
Dipl.-Ing. Rainer Millinghaus, Leiter für den Kabeltiefbau, Amprion GmbH
Dipl.-Ing. Timo Mücke, Bereichsleiter Großbohrtechnik, Beermann Bohrtechnik GmbH
Dipl.-Ing. Frank Platzbecker, Gesellschafter Ingenieurbüro H. Berg & Partner GmbH
Weiterlesen:
Neueste Beiträge:
Meistgelesene Artikel
Für welche Leistungsart interessieren Sie sich?
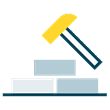
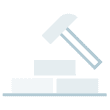
Bauleistungen
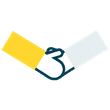
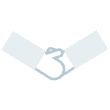
Dienstleistungen
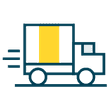
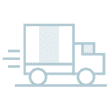
Lieferleistungen
Top Bau-Themen:
Aktuelle Termine für unterirdische Infrastruktur
25.08.2025 - 26.08.2025
Seminar Bedarfsorientierte Kanalreinigung10.09.2025
Norddeutsche KanalsanierungstageJetzt zum Newsletter anmelden:
Leitungsbau, Kanalsanierung, Abwasser – erfahren Sie das wichtigste rund ums Thema unterirdische Infrastruktur.