Direct in die Ems
In Rysum kam zum zweiten Mal weltweit Direct Pipe zum Einsatz. Da hier erstmals mit diesem Verfahren ein Produktenrohr verlegt wurde, hatte die Baustelle so etwas wie Premierencharakter.
PDF ansehen
Die EWE Netz GmbH hatte von der EWE AG und der Wingas GmbH & Co KG den Auftrag größere Teilstücke einer rund 40 Kilometer langen Sohleleitung zwischen den neu entstehenden Gasspeichern in Jemgum und dem etwa 15 Kilometer westlich von Emden liegenden Rysumer Nacken zu errichten. Ein Kernstück dieser Leitung ist ein etwa 200 Meter vom Ufer entferntes Einleitbauwerk, mit dem die ankommende Salzsole in die Außenems eingeleitet wird.
Auflagen der Genehmigungsbehörden hatten zur Folge, dass die etwa 280 Meter lange Anbindung dieses Bauwerks an die Soleleitung in einem grabenlosen Rohrbauverfahren hergestellt werden musste.
Bei der Leitung handelt es sich um eine Stahlrohrleitung DN 1200, in die später ein GFK-Rohr DN 900 eingeschoben wurde. Der Ringraum wurde verdämmt. Die Druckaufnahme in diesem System, >16 bar, wird nur durch das Stahlrohr sichergestellt. „Wir sprechen hier deshalb nicht vom einem Schutzrohr- sondern von einem Produktenrohrvortrieb“, sagt Thorsten Soppa, der bei der EWE Netz für den Bau und Betrieb von Hochdruckleitungen verantwortlich ist.
Randbedingungen sprachen gegen HDD
Für die Baustelleneinrichtung stand nur eingeschränkt Platz zur Verfügung. Ein etwa 60 Meter langer Streifen musste reichen, um die Maschinentechnik unterzubringen und den Rohrstrang vorzustrecken. Wegen des engen Terminplanes musste das Einleitbauwerk parallel zu der Anbindungsleitung errichtet werden. Dies erforderte eine hohe Zielgenauigkeit des Vortriebes mit einer Toleranz von wenigen Zentimetern. Ein Einziehen des Rohrstranges von der Wasserseite war aus Platzgründen und wegen des Schiffsverkehrs auf der Außenems ausgeschlossen.
Diese Randbedingungen stellten entsprechende Anforderungen an die Wahl des Bauverfahrens. Es musste einen sektionsweisen Vortrieb zulassen, mit der Möglichkeit, die einzelnen Rohrabschnitte für den Vortrieb vorbereiten und mit dem Rohrstrang verbinden zu können.
Vor diesem Hintergrund schied das HDD-Verfahren aus. Die geringe Überdeckung zwischen Rohr und Grund der Außenems von nur 3 Metern, die hohe geforderte Zielgenauigkeit und die fehlende Möglichkeit, den Rohrstrang seeseitig einzuziehen waren Umstände, die ebenfalls gegen das HDD Verfahren sprachen. Übrig blieb das klassische Microtunnelverfahren und das neue, bisher erst einmal eingesetzte Direct Pipe Verfahren.
Neues Verfahren mit bewährter Technik
„Direct Pipe ist nicht mehr und nicht weniger als die Kombination bekannter Bauverfahren, nämlich dem Microtunnelling und dem HDD-Verfahren“, sagt Dr. Rüdiger Kögler. Von ihm stammt die Idee für dieses einstufige, grabenlose Verlegeverfahren.
Die Produktrohr-Pipeline wird vorgeschweißt, geprüft und auf der Startseite auf Rollenböcken gelagert. An der Spitze des Rohrstranges wird eine Microtunnelling-Maschine installiert. Als Vorschubeinheit fungiert der an der Startgrube aufgestellte Pipe Thruster, der die Pipeline von außen umfasst und schubweise sowohl Maschine als auch Pipeline in den Boden vorpresst. Ein wesentlicher Vorteil des Pipe Thrusters gegenüber normalen Microtunnelling-Pressenrahmen ist die Möglichkeit zum Vorschieben von Endlosrohren.
Der Abbau an der Ortbrust wird wie beim Rohrvortriebs-Verfahren von einer Microtunnelling Maschine ausgeführt. Das Schneidrad kann auf die jeweilige Geologie abgestimmt und mit entsprechenden Abbauwerkzeugen bestückt werden. Dadurch können im Gegensatz zu HDD-Verfahren auch größere Steine, härtere Geologien aber auch nicht standfeste Geologien (Kiese) durchfahren werden. Die Ortbrust wird bei Bedarf mit einer Bentonitsuspension flüssigkeitsgestützt. Der Materialabtransport erfolgt über einen Flüssigkeitskreislauf mit zwischengeschalteter Separationsanlage, die das abgebaute Bodenmaterial von der Spül- und Förderflüssigkeit trennt, bevor diese über Speisepumpen wieder der Ortsbrust zugeführt wird. Die Steuerung der Maschinentechnik erfolgt vom Steuercontainer aus. Die Vermessung der Vortriebsmaschine wird über einen Kreiselkompass und einem separatem Höhensensor vorgenommen.
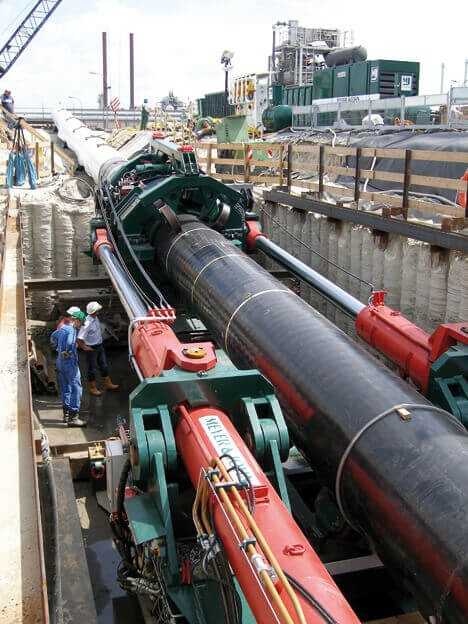
Vorteile für Direct Pipe
Dr. Kögler sieht Direct Pipe als ergänzendes Verfahren zu HDD und Microtunnelling für die Verlegung von Stahlrohren mit Durchmessern zwischen 800 und 1400 Millimetern und Verlegelängen bis 1000 Meter. Im Vergleich zum HDD kann Direct Pipe nach Dr. Köglers Einschätzung in schwierigeren Geologien respektive mit geringerem Baurisiko eingesetzt werden. Außerdem sieht er in Direct Pipe eine wirtschaftlich interessante Perspektive, da hier gegenüber dem HDD Verfahren drei Verfahrensschritte – Pilotbohrung, Aufweitung und Rohreinzug – in einem Verfahrensschritt zusammengefasst werden. Einen weiteren Vorteil sieht Kögler in dem Umstand, dass bei Direct Pipe nur von einer Bauseite gearbeitet wird. Eine „Pipesite“ wie beim HDD mit entsprechender Baustelleneinrichtung entfällt. Das vermindert den Aufwand insbesondere bei Sea Outfall Leitungen erheblich.
Grundsätzlich gilt im Wirtschaftlichkeitsvergleich Direct Pipe vs. Microtunnelling: je mehr Platz zum Vorstrecken des Rohrstranges desto weniger Kopplungspausen, desto höher die Geschwindigkeit, desto wirtschaftlicher wird Direct Pipe. Bei der Maßnahme in Rysum konnte Direct Pipe gegenüber dem Microtunnel bereits seine Vorteile ausspielen, obwohl der Rohrstrang wegen der beengten Platzverhältnisse in Segmente von 36 m Länge unterteilt werden musste. Weil jedoch ein Schutzrohr aus Stahlbetonrohren entfiel, dadurch der Bohrlochdurchmesser deutlich geringer war und ein Verfahrensschritt, nämlich das Einziehen des Stahlrohres in ein Schutzrohr, eingespart wurde, war Direct Pipe unter dem Strich das günstigere Verfahren.
Sicherheitsreserven
Die Maßnahme in Rysum war bisher weltweit die zweite Direct Pipe Baustelle. Für Thorsten Soppa als Auftraggeber war dennoch die Risikominimierung neben der Wirtschaftlichkeit ein entscheidendes Argument für die Auftragserteilung. „Wir hatten nur den einen Versuch und wäre der Fehlgeschlagen hätte dies ein Jahr Zeitverzug für den Solbeginn der Gasspeicher und einen immensen wirtschaftlichen Schaden zur Folge gehabt.“
Den Auftrag für die vom Ingenieurbüro de la Motte und Partner geplante Maßnahme erhielt die Firma Meyer & John. Das Hamburger Unternehmen hat in das neue Bauverfahren investiert, um sich neue Marktsegmente zu erschließen und so sich den geänderten Anforderungen besonders im Versorgerbereich verstärkt zu stellen. Meyer & John verfügt über zwei Pipe Thruster mit 500 und 750 Tonnen Schubkraft.
Rohrpost abonnieren!
Wir graben für Sie nach Neuigkeiten. Die Ergebnisse gibt es bei uns im Newsletter.
Jetzt anmelden!
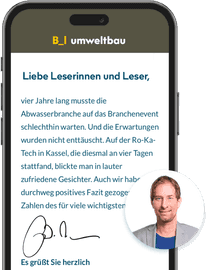
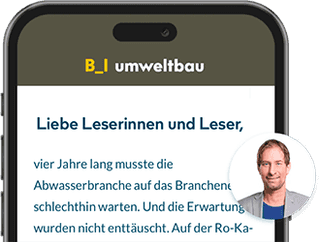
Die eigentlichen Bauarbeiten begannen mit der Herstellung der Baugrube und dem Aufstellen des Pipe Thrusters. „Das war schon so eine Sache für sich“ erinnert sich Johannes Müller, Abteilungsleiter bei Meyer & John. „Der Thruster mit 750 Tonnen Schubkraft wiegt aufgebaut 85 Tonnen. Gerechnet haben wir mit Schubkräften von 500 Tonnen, aber diese Kräfte wollen auch erst mal in den Baugrund eingeleitet werden.“
Der Vortrieb mit einem vertikalen Radius von 1400 Metern erreichte das Ziel mit einer Abweichung Null Millimetern in der Höhe und von 2,4 cm in der Horizontalen. Für die 36 Meter langen Rohrsektionen benötigte die Vortriebsmannschaft im Schnitt vier Stunden. „Wobei der begrenzende Faktor die Leistung der Förderpumpen für den Abraum war“, betont Dr. Kögler. Bohrkopf und Steuerungstechnik hätten durchaus noch höhere Vortriebsgeschwindigkeiten zugelassen.
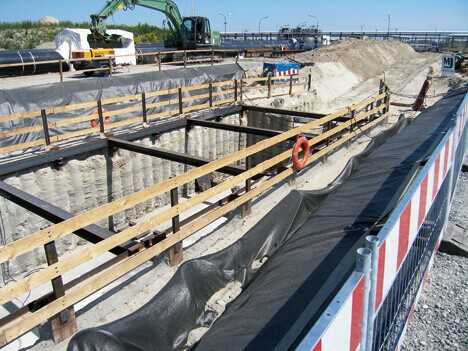
Die Presskräfte lagen während des Vortriebes im Schnitt bei 100 Tonnen. Der absolute Höchstwert lag kurzzeitig während des Anfahrens bei 270 Tonnen.
Auch der Baugrund hielt Überraschungen bereit. Zwar war ein Baugrundgutachten Bestandteil der Ausschreibung. Zwischen den Untersuchungspunkten traf der Vortrieb jedoch auch auf Holzbefestigungen und eine Steinschüttung. Umstände, die anderen Bohrverfahren Probleme bereitet hätten. „Hier bestätigte sich unsere Risikobetrachtung, die davon ausging, dass Direct Pipe bei unvorhergesehenen Zwischenfällen während des Vortriebes die größten Sicherheitsreserven bietet,“ erläutert Thorsten Soppa und Johannes Müller ergänzt: „Im schlimmsten Fall bietet dieses Verfahren ja sogar die Möglichkeit, den Rohrstang wieder aus dem Bohrloch herauszuziehen und gegebenenfalls mit neuen Abbauwerkzeugen auf unvorhergesehene Besonderheiten des Baugrundes zu reagieren.“
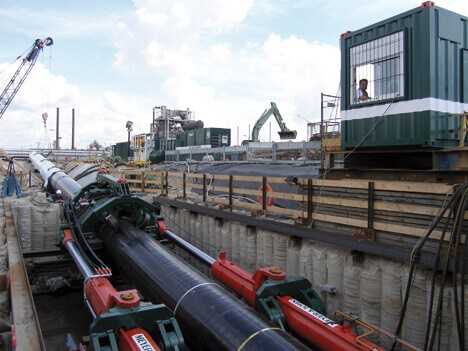
Weiterlesen:
Neueste Beiträge:
Meistgelesene Artikel
Für welche Leistungsart interessieren Sie sich?
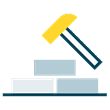
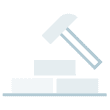
Bauleistungen
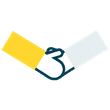
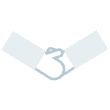
Dienstleistungen
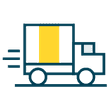
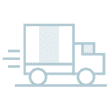
Lieferleistungen
Verwandte Bau-Themen:
Top Bau-Themen:
Jetzt zum Newsletter anmelden:
Leitungsbau, Kanalsanierung, Abwasser – erfahren Sie das wichtigste rund ums Thema unterirdische Infrastruktur.